Robots in Paradise
Sometimes everything lines up
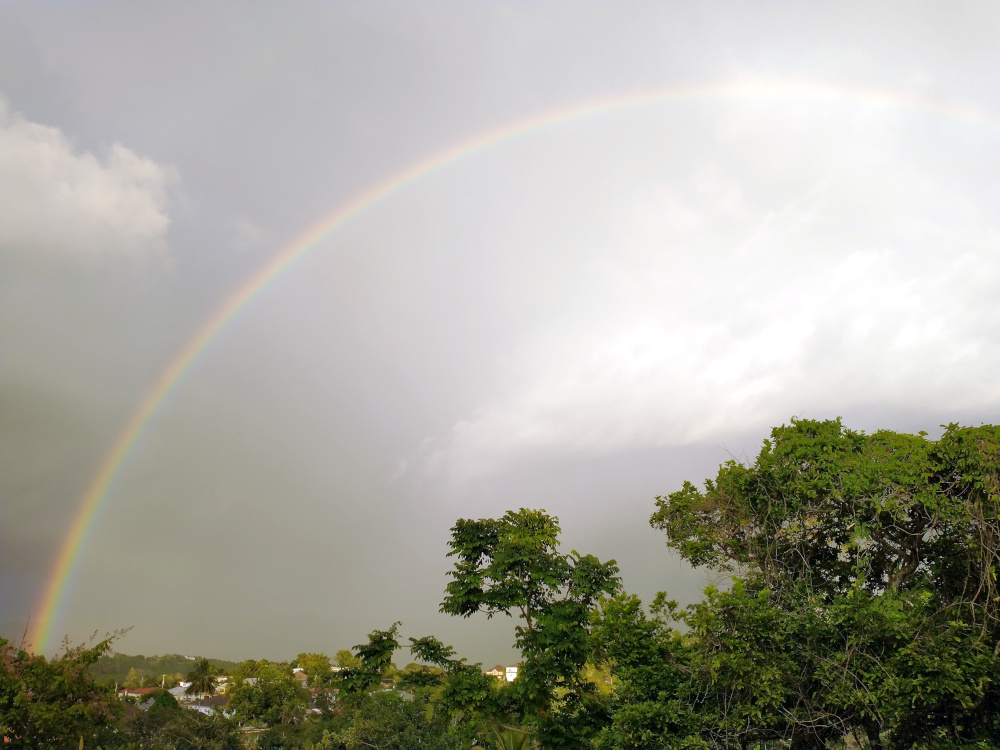
Patience is a lesson taught early in the jungle. Everything takes time, be patient, work hard, and it will all come about. This spring Apollo is moving around nicely with the Propeller micro-controller inside, reading new position data once a millisecond from the Pi and sending it out to the stepper motor drivers 200 times in a millisecond to make nice smooth motions.
Apollo 10 L & M
Pictured on the left side of the image is a long-arm Apollo variant, setup as a camera robot, to take videos for marketing. The long-arm version uses the same frame, motors and controller as all versions of Apollo 10, it just has longer arms.
Any Apollo 10 can be switched between Short, Medium and Long arm versions by the user. It takes about 30 minutes to make the switch, unbolting the old arms, and bolting in the new ones.
Pictured on the right side of the image is a medium-arm Apollo, the standard length version. Both robots are mounted on stands built of 80/20 Aluminum Extrusions, a popular robot mounting method used in factories around the world.
Old Harbour Bay Fishing Village, a great spot to find fresh local seafood on the south coast.
Frame Dry-Fit
Long Arms in Fixture
Installing Arms
Assembly of a long-arm variant of Apollo 10, used as a camera robot above. First the frame is dry-fit, to make sure everything fits nicely, and all the necessary parts are on hand. Second a pair of arms are getting epoxied in a long-arm fixture. Third the arms are being installed after the motors and other hardware.
Leadshine iCS-2313
A Stepper Motor with Encoder and Driver built in. These motors are currently being tested on the camera robot. They have a larger 8mm (vs 6.35mm) shaft than the standard motors, and require a different bore timing pulley. The motors work spectacularly though, as Leadshine motors always do. The encoders do a nice job bringing the motor back to the correct position if it has been pushed past its limits temporarily.
Once the frame is assembled and the motors / hardware have been installed, all the electronics go inside. One wires up the stack of electronics, tests it, and then fits it into the robot where it is enclosed and cooled with filtered air for safety.
A Jerk Pan (BBQ Grill) getting its bottom half replaced with a nice fresh piece of a 55gallon Tolulene Drum.
Westmoreland Jamaica, looking north over the mountains.
ServoCity Servo Gearbox
Opened Up
Powering a Rotary Axis
Now that Apollo is working smoothly with supply-chain issue resistant parts, its time to use it. One puts End of Arm Tooling (EOATs) on the End Effector for various tasks. Pictured is a Servo Gearbox purchased from ServoCity with a goBilda servo inside, used as a rotary axis on the end effector. It adds more rotation to the EOAT. All builds pictured will be explained in the Docs section of oshRobot.com
Solenoids
To control vacuum and pneumatics (compressed air), two solenoids are placed on the robot. These are actuated by two relays, driven by an Arduino Nano RP2040 Connect. This particular Arduino supports ROS (robot operating system). ROS also runs on the Pi and sends signals the user inputs via Gcode or the GUI to the Arduino to execute.
Pictured below, a stand being built for Apollo of 80/20 Aluminum Extrusions and joining components. This stand sits above a vacuum table with aluminum honeycomb for laser-cutting operations. A build thread will be included in the docs. The table is 45 inches wide and long, a nice size for the Medium Arm variant of Apollo 10.
When a robot is setup to complete a specific task the process is called integration. The Apollo 10 pictured is being integrated to be a pick and place machine. Note the solenoids attached to the frame, and rotary axis on the end effector with vacuum gripper.
80/20 Aluminum Stand
Integration